We can provide aluminum alloy ingots with the following:
97-98% soft aluminum
aluminum casing
silumin shell
silumin injection
Alcoa 380
Alsi 132
As 10 g
Links mothers aluminum base.
STANDARDIZATION
|
Si
|
Fe
|
Cu
|
Mn
|
Mg
|
Ni
|
Zn
|
Cr
|
Ti
|
Sr |
CARTER
|
SAE 322
|
2-4.10
|
0.50-1.50
|
1-2.10
|
0.50-0.80
|
0.20-0.50
|
0.10-0.20
|
1.50-3
|
- |
-0.25+
|
- |
ALSI
132
|
. |
11-12.50
|
0.7-1
|
1.75-2.50
|
0.50
|
0.30
|
0.30
|
1.40
|
- |
- |
- |
SILUMIN
COQUILLA
|
. |
12.50-13
|
0.50
|
0.50
|
0.50
|
0.10
|
0.10
|
1.10
|
- |
0.10
|
- |
ALCOA
380
|
SAE 309
|
8-9.50
|
0.70-1
|
3-4
|
0.50
|
0.30
|
0.50
|
1.40
|
- |
- |
- |
AS 10
G
|
. |
9-11
|
0.50
|
0.20
|
0.25-0.45
|
0.30-0.50
|
0.05
|
0.30
|
- |
0.15
|
- |
AS 10
G CON ESTRONCIO
|
SAE 323
|
9-11
|
0.50
|
0.20
|
0.25-0.45
|
0.30-0.50
|
0.05
|
0.30
|
- |
0.15
|
0.30-0.60 |
SILUMIN
INYECCION
|
. |
11-13
|
0.7-1
|
0.50
|
0.5
|
0.10
|
0.10
|
0.20
|
- |
- |
- |
Aluminum alloys. The alloy chosen is determined by:
Mechanical properties requested
Workpiece thickness
Application or use of the piece.
Other specific parameters requested by the client.
Within these ranges of alloys, the most common are:
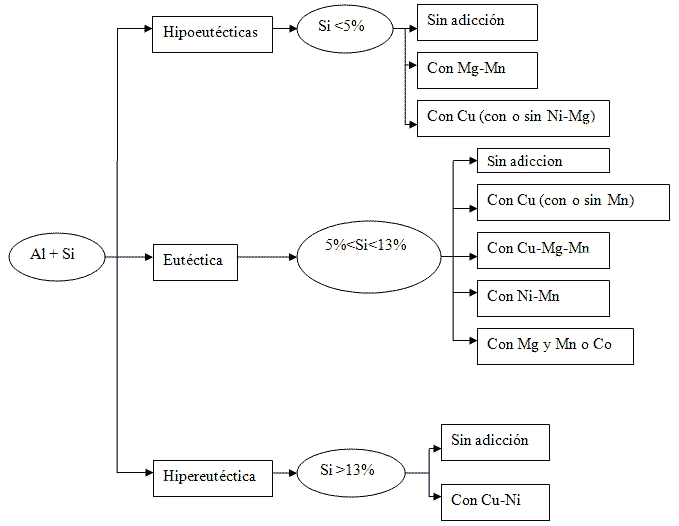
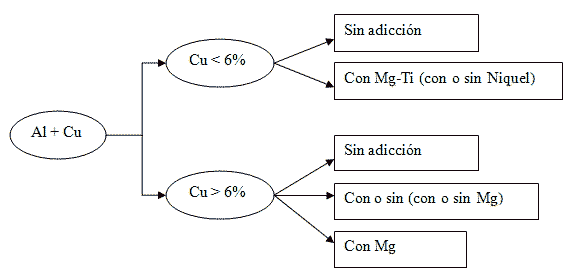
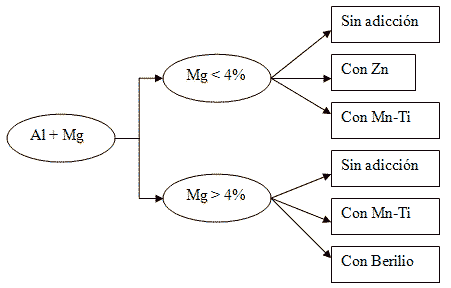
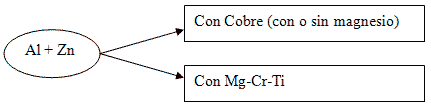

Some basics about aluminum base alloys and the influence of alloying elements or impurities:
Pure aluminum has limited uses, to improve their mechanical properties and castability it, adding other metallic elements such as: copper, silicon, magnesium and to a lesser extent manganese, iron, zinc and nickel. The effects of the alloy are as follows:
Copper:
Raise the mechanical strength (even hot) and hardness, improves the fluidity and machining.
They are susceptible to heat treatment.
Silicon:
It is the most important element of addiction to aluminum because it improves the characteristics of the casting, the fluidity increases, decreasing the fragility hot and solidification shrinkage, improves resistance to corrosion.
Machining is difficult, when the percentage is around 13% should modify its structure with strontium or other salts.
Magnesium:
Increases strength, hardness, corrosion resistance and improved machining.
Be very careful in handling the liquid metal, since it is easily oxidized and therefore lose the metal.
Alloys containing silicon and magnesium can be heat treated.
Iron:
It is a natural component of aluminum, also is built into the main alloying the silicon as an impurity.
In a small percentage increases strength, hardness and decreases the tendency to hot cracking.
Because of the way in which they find in the alloy (needles and platelets) should always be in the presence of manganese, chromium or copper.
The percentage is acceptable according to the method of manufacture, since their separation depends on cooling rate, hence the lower the percentage accepted for castings on the ground for mold.
Manganese
Their presence should never exceed 0.50% and it is essential that in alloys with iron to form a composite Al-Fe-Mn, which improve the mechanical properties and machining.
Zinc:
While percentage is up to 2% does not affect the characteristics of the alloy, increasing the density, low thermal resistance and increases the stress corrosion cracking susceptibility wing on that ground should be limited in their presence.
Nickel:
The reason for their addiction is to improve the hot strength.
Titanium
Its main action is to refine the grain. Mainly by improving their mechanical properties, its tensile strength and fatigue, it also creates a smoother surface.
Source: Figures (Foundry Industry Chamber of Argentina)
There are more technical information about this product to request call 4721-9391 / 4756-3084 or via e-mail to ventas@mazzola.biz.
|