Kurtz offers high technology for metal smelting, high quality standards and a solution for each client. Kurtz metals, founded in 1779 in Germany today is a multinational company with over 850 employees worldwide.
Kurtz metal produced:
1 - Injection of low pressure.
2 - gravity casting machines.
3 - deburring presses
4 - Robot interface.
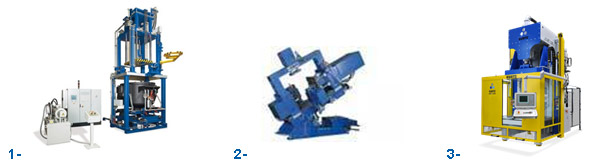
Casting process for low pressure - controlled mold filling, solidification controlled high-efficiency.
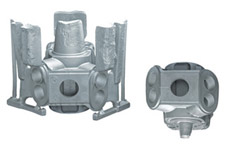
Low pressure metal matrices (left), low pressure sand packages (right)
The process of low pressure casting is predestined to perform very high demands on quality. This pressure charging the furnace, molten aluminum goes through the standpipe inside the shell. With rising pressure controlled and mainly uniform, slowly fill the hole in the mold and prevents the formation of skin oxidation, creating cold welding and the risk of air inclusions.
During every phase of solidification, the furnace pressure is constant and produces safe food and dense castings. Thanks to measures of casting technology and employment targeted cooling of the mold, it reaches an optimal directional solidification.
With its start casting box innovative KURTZ offers flexibility so far unknown in the attack and feeding pieces through the process of low pressure casting - regardless of the geometry of the part to be cast and without additional input from Calos . In this process the number of inputs and food is not limited and can therefore put many small cross-sections of local effect. It has also been also credited the use of one or more tubes studs.
Comparison of gravity and low pressure casting process, reducing yields:
before: part weight: 21.3 kg, output: 54%, after: part weight: 12.2 kg, output: 92%
In addition, as a rule, production increases, because the process is more reproducible and less dependent on external influences. Whether it is a classical part with rotational symmetry, or components that require a complex attack system, no matter what you have to strain, KURTZ always offers the right solution for low pressure die casting.
Aluminium alloys.
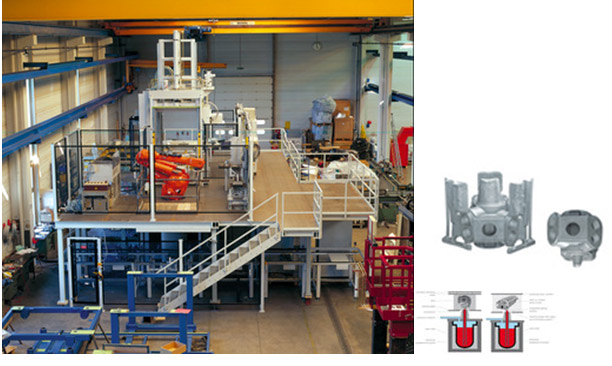
Máquina para fundición de aluminio a baja presión con robots de manipulación, equipos periféricos y tecnología de transporte.
Compared with gravity casting, low pressure casting offers the following advantages: low pressure casting, the metal in the furnace is pressed through the riser and into the mold by the pressure acting on the surface metal (Figure 1). This form of mold filling is the most important difference with respect to gravity casting and foundry swingarm. The mold filling process is completely controlled. This results in a very low or no turbulence during mold filling.
The metal in the furnace is in a closed vessel under a protective atmosphere. As a result, the merger reduces their exposure to impurities such as hydrogen and others, and thus reduces the formation of oxide layers. That's the key to good melting quality.
Unlike gravity casting, the metal surface is not continually interrupted during the filling process, since low-pressure filling is made from top to bottom. The result is again the clean metal. Especially the filling of the mold section is repeatable and executed directly by the machine and thus no longer depends on the "founder with his spoon." Operator errors can be minimized by an automated process.
One of the main advantages of low pressure casting of the intake system is lower compared with gravity casting. The feeders are usually not necessary, which reduces the material cycle. The low pressure casting, the material cycle is 5% to 20% by weight of the foundry, while the cast of gravity that can reach up to 100%. The material also means lower costs for cleaning, cutting and merging in general, can be reduced significantly. The cleaning costs are mainly staff costs, especially for small foundries, for whom the automatic cleaning or drill press is not profitable at all. Given the current and future increases in energy costs (which has an incidence at $ xx / kg of fusion), each kilogram of fusion should be avoided unnecessary.
The best price segment.
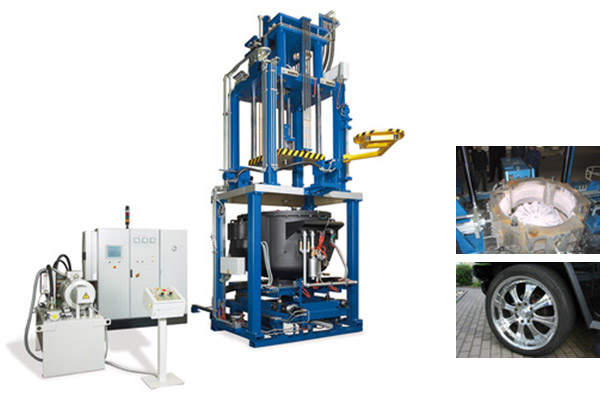
KURTZ AL SR 14-10 - modelo básico con un alto estándar de calidad a nivel de precio asequible
The best quality at the best price: low pressure casting machines for high volume production
The latest addition to the family of KURTZ foundry machines is a new machine at low pressure in the low price segment of the market, designed for high volume production of standardized products, such as wheels.
However, the low price segment is far from cheap, customers can still expect the quality standard known KURTZ. The pressure control system KURTZ is the key to the process and is the most accurate on the market.
In addition, KURTZ AL 14-10 SR stands for offering easy handling and ease of use. This is made possible by the use of standardized components, which affects shorter delivery times and installation and commissioning of the machine faster.
High volume.
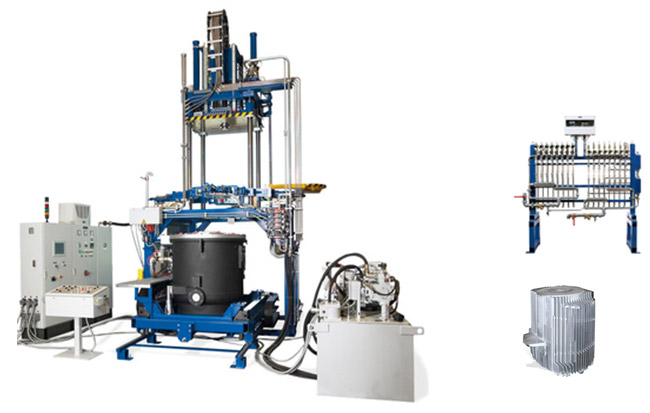
Low pressure machine for aluminum to 10/07 SC - very flexible, furnace exchange systems
Under Pressure - High Quality
KURTZ technology for oven-sharing systems.
Especially in the area of low pressure casting, the solutions KURTZ enjoy an excellent reputation due to the low pressure KURTZ machines are designed to meet the highest standards of quality. There are basically two different designs: machines with a clamping unit with a fixed or mobile maintenance oven - called S versions allow you to increase accessibility for maintenance and allow the use of interchangeable furnace systems with cranes, trucks , transportation fro oven. The S series machines can be equipped with a crucible or Cuba the desired size.
The second version is for machines with clamping unit and a tilting crucible furnace fixed - called TC Series - are especially suitable for small foundries with frequent changes of alloy.
KURTZ foundry machines are well known for their innovative designs. The design of four pillars, along with the parallel guide, ensure a correct closure of the mold. For the operation of the mold side segments, Kurtz offers a number of cores. For an automated casting cycle, the machine has mechanical or hydraulic ejectors and a collection device integrated piece. The oven is uniformly docked to the shell by rising spindles. The design of the coupling system allows for flexible application of the riser pipe and several boxes of food designs. An optimized cooling of the mold not only ensures the controlled solidification, but also increased productivity due to shorter cycle times. Due to the use of high quality parts, cooling measures can be established in a reliable and reproducible. The service staff is constantly informed of the ongoing process parameters through a monitor. At the same time, cycle-related data are collected and stored for later analysis of quality.
All KURTZ foundry machines are easy to use, handling and control as well as the ability to store and activate quality recipes. The modular design of the casting machines with many accessories and peripherals provides a high degree of automation, reproducibility and management for maximum quality. The optimal design of the caster low pressure depends on the needs of customers. Technology offer low pressure casting, with the slogan: "Under Pressure - High Quality"
Tailored Solutions.
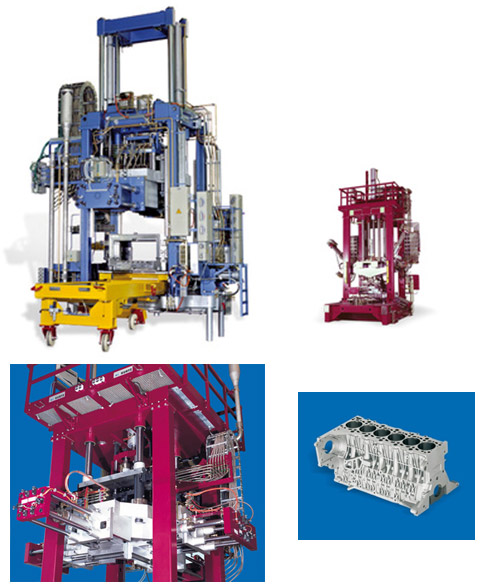
Low pressure casting for runners not only powerful.
"What Standrad not enough by itself and we can not just be cheap either." Are needed real solutions to customer requirements. Thanks to the broad composition of the team of Kurtz and synergies with its own cast aluminum, Kurtz has been able to acquire an excellent reputation in the customers through specific special solutions.
This is corroborated by customer references, such as BMW, KS ATAG, Honsel, runewald or Mahle. The application spectrum of KURTZ foundry machines of low pressure extending from rapid prototyping through the casting series so special solutions, for example, cast crankshafts cylinders. Strain constructions both coreless or male (open deck design) and closed cover designs, where the management of the water jackets are an additional requirement in the process. The machines are equipped with cores for the foundry, so the precise guidance of the dampers is a special construction details. KURTZ Especially in the field of automotive suppliers, the cells of low pressure casting KURTZ increasingly used.
The expression "every shot has to hit the target" is above all for the rapid prototyping field of components for the automotive industry. Here the key to success is the quality of trust and reliability terms. These sand molding systems LP-They are neither far as spectacular as the big systems, but no less efficient. The exact correspondence of the rising level of molten metal with the pressure curve is pre-programmed the most important criterion. KURTZ control system establishes the rules regarding the accuracy and process safety.
The highest quality of metal is accomplished through an exchange system oven. The trend is in addition to low pressure casting of parts in basic packages of sand cores and sand molds. Here, Above all, the high quality metal and the low turbulence fi lling of the mold are Ideally use. Here we take advantage of, especially, the quality of metal and filling the mold with little turbulence. The process is suitable for the small number of parts to an automated mass production. Here, metal smelters Steinruck, Becker and Grunewald CCC may be appointed as experts Kurtz.
In general, products for low pressure casting of aluminum are safety relevant parts, which require especially high quality, whose demands are the highest priority. These may, for example, chassis or engine parts. Moreover, the melting process of low pressure is also for pressure-resistant components with the highest load demands in vacuum technology and hydraulic technology.
That's how KURTZ offers Countless individual engineering solutions for low-pressure casting, always Faithful to the motto: Everything from one mold! This is how KURTZ offers a number of engineering solutions, individual low-pressure casting, always faithful to his motto: All from a mold!
Casting lines.
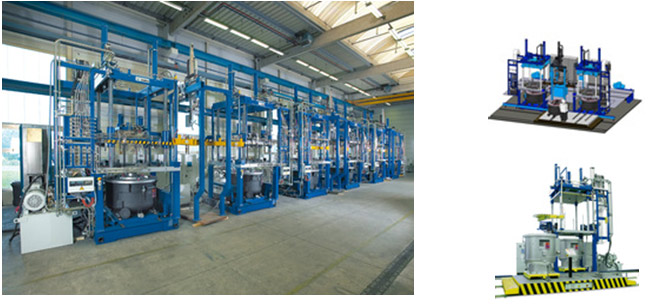
Complete solutions for mass production.
For mass production of a wide range of demanding KURTZ offers a complete line of cast iron. They may, for example, be equipped with furnace exchange systems. This affects the time of extremely rapid change in oven in a metal bath of excellent quality and reducing defects start after changing furnace.
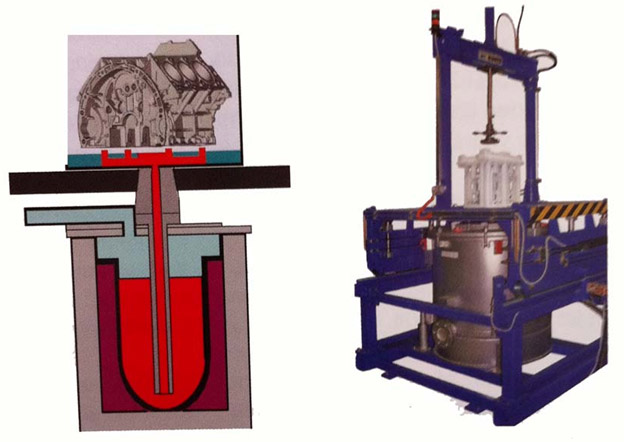
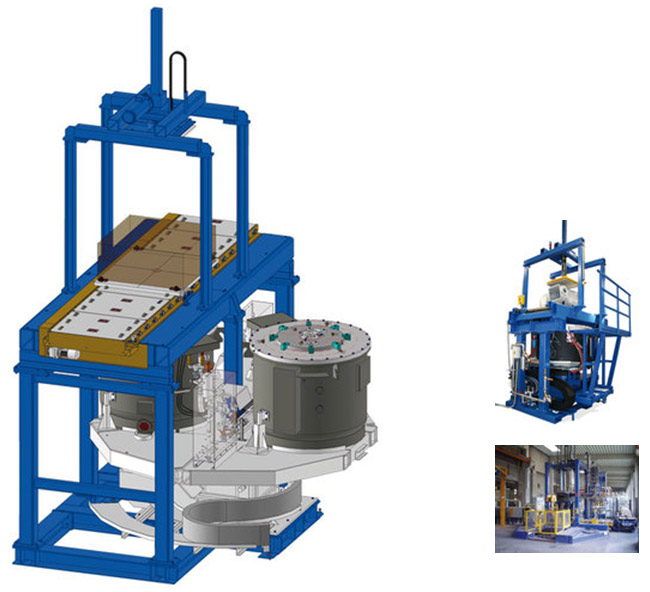
Low pressure machine KURTZ aluminum sand molds with the change dish from the oven.
Challenging sand casting - from rapid prototyping to series production.
There are several good reasons to choose the application of sand molding machine KURTZ. As the technology of low pressure casting Kurtz in the highest echelons of international competition. Several teams already have the advantages of controlled mold filling and produce their prototypes and racing engines in machines Kurtz.
The automotive industry is not the only sector that is interested in the technology of low pressure KURTZ. Other industries include aerospace and ultimately anywhere every gram counts in order to maintain the mass of moving parts to a minimum. In this context, the casting of magnesium becomes more and more interesting.
For now, aluminum is not the only molten metal casting machines KURTZ low pressure. This casting technology also has enormous potential in aluminum bronze parts for the marine industry to magnesium for lightweight construction in general.
In general, sand casting machine KURTZ offer a wide scope: from chemically bonded sand molds, buildings with green sand molds plaster molds for special pieces with high demands on precise details. In the fine pieces in ceramic molds are made possible fine structures up to 1 mm wall thickness.
Molds different - different parts. The product range includes everything from small parts with only a few kilograms to 260 kg carcass weight of cast iron, from individual pieces to prototypes to mass production.
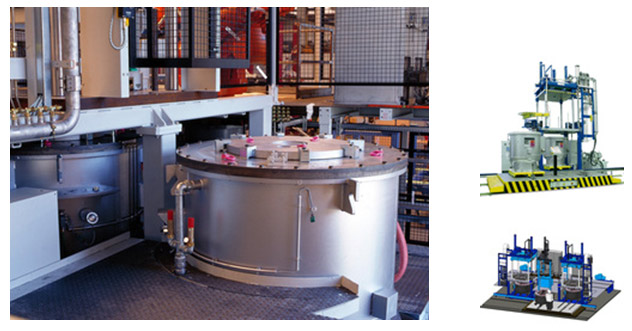
Oven interchangeable turntable.
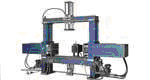
The gravity casting machines.
In general, gravity casting is the traditional casting process. Practiced for centuries, it still offers potential for improvement.
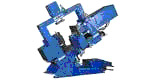
Rocker molding machines by gravity.
Just as the Bavarian Weissbier pours his expert in glass, casting machines, molten metal KURTZ fill the mold with low turbulence. The rate of freely programmable tilt allows optimum filling rate
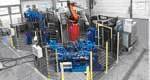
All inclusive solutions
KURTZ offers tilting gravity and gravity casting machines, which are available as a single machine or turnkey solutions complete / whole cell casting. The flexible machine concept is easily adapted to different requirements of customers.
Casting process.
Gravity casting machine KURTZ
The cores make the difference
In general, gravity casting is the traditional casting process. Practiced for thousands of years, still has potential for improvement. Kurtz has developed a machine concept, especially for foundries request. Due to the modular machine concept can be used universally. What is needed is flexibility with respect to various foundries. The conversion must be possible without great effort. And KURTZ machines easily meet these requirements. By adding additional cores and closing units, the basic machine is suitable for the demands of the smelter complex.
Two casting molds run on the stage of a machine. This leads to greater productivity with the added advantage of less space required and understaffed.
The unit offers opportunities as mobile hydraulic control of mo-bile and hydraulic power unit for control of the foundry closing and opening of proposals for a maximum of two casting machines.
All gravity casting machines are equipped with the control system of proven effectiveness, which is also being used in machine types. The program of the machine controls the sequencing process and the movement of the cores. In addition, links the control of the machine with an external control system to manage processes in a cell full cast and offers operational possibilities in large-scale production.
KURTZ Trimming presses
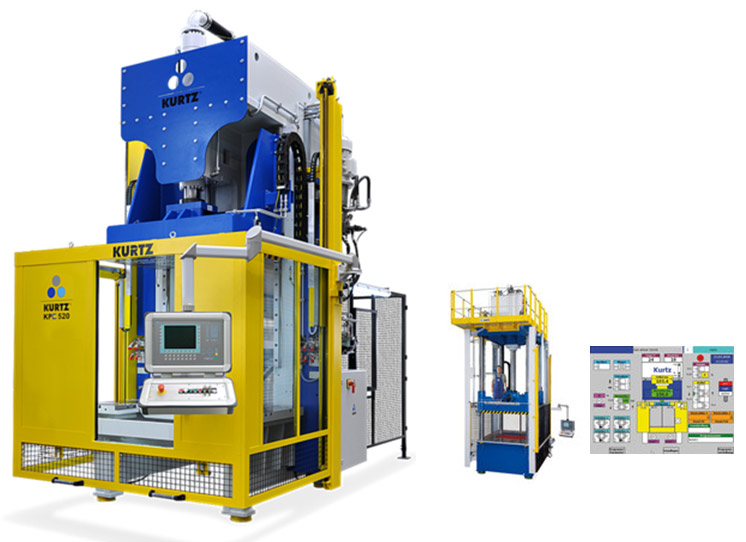
KPC 520: C-frame press with a pressing force of 52 tons, suitable for manual loading and manipulation of the robot
Deburring cost-effective solutions - technology for all applications
Besides the conventional manual deburring, there are highly cost-effective solutions, automated.
An important part in cutting technology is the cutting press, including the mold. KURTZ presses can be used with the molding process from high-pressure, low pressure and gravity.
Depending on the application, Kurtz offers press clipping C-shaped structure, like version in the form of columns and frame construction. KURTZ presses can be equipped according to customer needs with accessories such as slides, rams, collection devices, blowing and lubrication. In addition, the board can be used with a tilt, movement or tilting of the sliding table and is available for all designs of the press.
KURTZ trimming presses are characterized by their innovative technical solutions. For example, the career of the ram press and are fitted with wear-free measurement and non-contact measurement. These systems are adjustable through the control system of the press and its visualization.
The hydraulic press is equipped with proportional valve technology. Hence the expulsion pressure can be chosen freely by the control system of the press. Additional energy can be saved by the ideal setting of the pressure curve of the pump and a function of time waiting at the pumps capacity.
The collection of castings is done through robust collection hopper with integrated blow molding strips, which for this are tilting and height adjustment without steps.
The press is controlled through a Siemens S7-300 - PLC with a user-friendly display.
|