Die casting machine Cold chamber
Frech offers cold chamber die casting machine with locking force between 2750 kN and 52,000 kN, which is used to melt small pieces purchased, as well as engine blocks and transmission cases, not to mention the components of the chassis and body aluminum alloy or magnesium. Thanks to its patented Vacural, Frech is a world leader in manufacturing engineering of lightweight designs.
For special requirements, we are at your disposal for any question. Please do not hesitate to contact.
The number of machines available are:
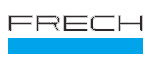 |
- DAK 250 - 1600
- GDK 2000 - 5000
- DualCast 2300 - 4000
- VACURAL Tecnología
|
DAK 250 - 1600
Frech cold chamber technology is setting trends for tight pressure and porosity free diecast objects.Frech cold camera technology, is at the forefront in obtaining parts free of porosity. In close cooperation with our customers We have Specially Developed the M-series machine to suit the growing range Demands of the market. Working closely with our customers, we developed a new program M series machines to meet increasing market demands.
The advantages of the cold room modular range Frech M Series are:
- Increased productivity through cycle time.
- Better quality foundry, with the highest rate of injection
- Complete flexibility for modifications and automation due to its modular design
- Possibility of combining different endings shooting and blocking units, more streamlined process for
- Option-L version available even with machines even larger plates
- Easy maintenance with easy access to all areas and remote technical support online.
- High durability and service life due to stable and robust construction of the machine.
- The modular system of the cold chamber injection Frech Frech M series is available to machines kN clamping forces from 2500 to 16,000 kN.
The M series machines are (2 Ton a 5 Ton):
- DAK 250
- DAK 350
- DAK 450
- DAK 580
- DAK 720
- DAK 880
|
|
- DAK 1100 (+ L-Version)
- DAK 1250 (+ L-Version)
- DAK 1400 (+ L-Version)
- DAK 1600 (+ L-Version)
|
 |
GDK 2000 - 5000.
GDK our machines with clamping forces of nominal value of between 20,000 to 50,000 kN set the standard for technology that puts a huge emphasis on customer requirements.
We believe that our core expertise lies not only in the construction of die casting machines, but also in developing solutions to specific problems, ranging from die casting machines to the formation of individual foundries fully equipped, turn-key hand (including molds).
Having worked on numerous projects for many years, we have developed a vast know-how. This means that we can offer expert assistance in the engineering of complex systems solutions, and application-specific advice for optimizing your casting process.
GDK 2000, GDK 2500, GDK 2800, GDK 3500, GDK 4100, GDK 5000.
DualCast 2300 - 4000
It's innovative die casting machine, with control of reliable technology, high-end shooting performance, and final design on the closing unit. Everything in the sound quality Frech, to meet future challenges.
- Floor space is limited
- Reduced operating costs
- Increased clerance tie bar
- Increased machine performance and reduced cycle time
- Simple and convenient mode of cores
- Flexible arrangement of boiler systems
- Optimized matrices Holding
- Easy adjustment of the height of mold
- Reducing setup time
- Innovative control concept
|
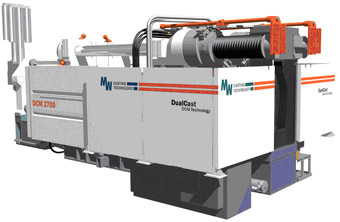 |
DualCast 2300, DualCast 2700, DualCast 3200, DualCast 4000.
Vacural Technologie.
Vacural The patented process is a tried and trusted has been used for many years to produce castings with a very low level of gas and oxide inclusions.
Structural and chassis components very ductile
Components with thin walls and welding
Parts coated surfaces
The low level of gas inclusions in the castings produced using technology greatly improves VACURAL the mechanical properties of the piece.
This makes it possible to ensure dynamic and static stability, and high ductility. |
|
|
Another strong point of Frech: competition for automation
The automation of a production process can make a difference in competitiveness, especially in regard to the reliability and reproducibility of a production cycle. Thanks to our own production development, and innovative partners that can ensure the highest quality with optimum economy.
It depends on the specific needs of your application, you can choose from the following accessories and technologies:
|
|
Moreover, the system of production control Datafrech specially developed for casting,
can help you with planning and real-time information of their production.
Furnace Technology
With experience Austrian Meltec oven manufacturer, Frech also has the know-how
required in the fusion and manipulation of non-ferrous metals and their alloys.
We have developed special technologies to achieve constant levels of the metal bath and stable temperatures, and to achieve cleaner alloys
Equipment for food and consolidating the fusion materials, along with magnesium dosing furnaces, complete the products offered by Meltec GmbH:
- Fusion single and multi-camera and holding furnaces for zinc, tin and lead
- Heated chamber furnaces for magnesium
- Magnesium dosing furnaces for cold chamber machines
- Preheating and charging devices for magnesium
- Fusion systems and feeding of zinc
Charger unit: Feedmat 1 + 2
Fully automatic dosing unit Feedmat motor provides high accuracy of dosing in a robust set of 2 arms. The control system easy to use and the flexibility to be used on either side of the vast majority of die casting machines, offers the perfect solution for the automation of production.
-
Simple adjustment and easy due to the configuration of the capabilities of the axes in3
-
Linear motion drives the vertical and horizontal for easy access to the sleeve injection machine
-
The bucket detects the metal bath level automatically with a precision metering + / - 2%
-
Feedmat 1 for up to 3 kg
-
Feedmat 2 for up to 12 kg
|
|
Heating and Cooling Units.
The temperature of the mold is a significant factor in relation to the casting quality and efficiency of the smelting process.
Robamat units of temperature control have been developed especially for the most demanding fields of application in the casting industry.
Heating and cooling units for heat exchange reliable, flexible in minimal space, oil-based heat transfer or pressure water system, designed as units of one or two circuits - the state of the art technology perfect for a sophisticated circuit.
Robamat heating and cooling units Warranty:
- best possible surface
- tight tolerances, even on complicated shapes
- continuous and sustained quality castings
- shorter cycle times
|
|
Lubrication unit 1 + 2
Our sprinkler systems for motor 1 +2 and continued development of various tools, spraying all the basic requirements of the most sophisticated technology of lubrication of molds:
- High positioning accuracy and repeatability
- High dynamics and high speed driving speed
- Powerful tools for lubrication of the more complicated geometries
- Optimization of the preparation of liquids and food
Lubrication unit 1
Shorter cycles require rapid lubrication systems, molds require complex solutions. With moves available from 400 to 1000mm, Lubrication Unit 1 is suitable for diecasting machines up to 5000 kN clamping force.
Lubrication Unit 1: 411E, 611E, 811E, 1011E
Moreover, we also offer simple pneumatic system of lubrication as a basic solution.
Lubrication unit 2
Lubrication system recently developed two axes meet ever increasing demands of position accuracy and speed of the dynamics operating within machine casting cold chamber:
- Hits from 800 to 1800 mm on machines up to 20,000 kN
- Similar linear units for horizontal and vertical axis
- Both axes driven by highly dynamic servo
- Freely programmable motion and time
Lubrication unit 2 : 864/600E, 1064/800E, 1264/1000E, 1464/1200E, 1664/1400E, 1864/1500E |
|
Extraction Unit: Gripmat 1 +2
The mold protection requires the utmost precision, productivity in casting requires a fast and reliable production.
With a robust and stable models Gripmat 1 + 2 are suitable for die casting machines hot chamber and cold
and ensure that the movements are precise with a positive and safe removal.
Gripmat 1 machines from 100 to 400 kN clamping force
Gripmat 2 machines from 400 to 800 kN clamping force
advantages:
- easy setup
- Fast, precise gripping and control of injection
- 3 optional motion sequences
- Electrically operated
- tire grip
- robust
|
|
Weight detection device. Weightcontrol 2000
This device controlled by a microprocessor weight detection guarantees mold protection and quality control for cast parts up to 2000 gr. 2000 gr.
Within the tolerances introduced by the user, which ensures a reliable verification of weight and communicates it to the casting machine.
features:
- weight detection cell
- Temperature compensation of position
- Operator input
- LED Display LED-Display
- Weight in grams-Display
special benefits:
- Standby function after weighing
- Automatic zeroing
|
|
conveyors
Conveyor belts made of sturdy construction, temperature resistant, with stainless steel cables as standard are available in various designs to further automate its production process. Depending on your particular application, we can also install a tunnel or an air cooled cooling water tank onto the conveyor.
We can offer the right solution for your needs:
-straight conveyors
-Protractors or type 'S'
-With or without refrigeration / cooling
- Various sizes available
Frech conveyor belts - keep your production moving!
DMT - Data Management Tool
DMT is a modular software system for data management developed by Frech for foundries pressure injection.
The different stages of expansion allow individual settings depending on the requirements of the smelter.
All work-related data are transferred via Ethernet from caster Frech, the DMT system.
The data management tool Frech DMT Data Management Tool Offered in 3 individual is stagesFrech expansion DMT is offered in 3 individual stages of expansion:
- Basic Version DMT PQ: Data Capture
- Expansion of the DMT version PQ-SPC: Data Capture and Analysis
|
|
Customer satisfaction is our priority.
Do not leave success to chance. Clearly, our scope is not limited to the manufacture of die casting machines of the highest quality. From the point of installation, and through the longevity of the machine, we offer our clients a comprehensive service - particularly aimed at these factors, which guarantees them a significant competitive advantage:
- Long lifetime of the machine
- Disposition reliable service
- Production of quality-assured
- economic production
- Qualified service personnel
|
|
Die casting machines in the House Chamber
With decades of experience and innovation in the manufacture of hot chamber machines for die casting, Frech has developed a unique knowledge of process technology. We developed a hot-chamber technology, able to meet all market requirements for casting. Our machines can produce functional parts with tighter tolerances, as well as decorative pieces, with an area of very high quality.
The lower specific pressure die casting hot chamber, offers the economic advantage of machines with a lower clamping force, but also faster production and less expensive.
The number of machines available are:
- Die casting machine hot chamber for Zinc (DAW-F)
- All electric hot chamber machines (DAW-E)
- Hybrid hot chamber machine (DAM-H)
-
(DAM-F) hot chamber machines for Magnesium (DAM-F)
Hydraulic Machines Hot Chamber Zinc (DAW-F)
Higher productivity and reliability are the result of decades of experience in the manufacture of die casting machines. Besides the design of the machine stable and robust, high dynamics of the new and improved final injection, meets all the requirements for perfect casting process.
- Cycle times even shorter by the new hydraulic system design block
- Easiest and friendly support and operation savest Remote Control with Datadialogy
- Operation easier and safer with the control system Datadialog
Simple operation based on Windows through the System Control Datadialog. |
|
DAW 20 F, DAW 50 F, DAW 80 F, DAW 125 F, DAW 200 F, DAW 315 F, DAW 500 F DAW 20 F, 50 F DAW, DAW 80 F, DAW 125 F, 200 F DAW, DAW 315 F, 500 F DAW
All Electric hot chamber machines (DAW-E)
The increasing demands of the economy and the environment are the basis of this product in new and innovative concept. With the all electric machine DAW type E, Frech new standards in September have hot chamber diecasting technology: With all types of electrical machines E DAW, Frech has set new standards in the technology of casting hot chamber:
- Environmentally friendly, with quiet and clean operation and no hydraulic fluidCuida el medio ambiente
- Energy-saving, due to lower power and water consumption
- Highest productivity due to shortest possible cycle-times
- Full real-time control of all movements with the easy adjustment of parameters
|
|
DAW 20 E, DAW 80 E, DAW 125 E DAW 20 E, 80 E DAW, DAW 125 E
Hybrid machine for hot chamber zinc or magnesium (DAM / DAW Hybrid)
The die casting machine hot chamber Hybrid unifies the advantages of the hydraulic injector with the injection power.
- Ideal for the production of functional parts within the tighter tolerances, and the highest standards of thickness and surface quality.
- The work of motorized axes can be synchronized or operate simultaneously - for maximum speed, accuracy and repeatability required. These strengths are of great importance in a fully automated cell injection.
The lower noise emissions and fuel economy of hybrid machine are very beneficial to the current demand for low stress levels and energy consumption in the workplace. |
|
DAM 200 H, 315 H DAM, DAM 500 H, 200 H DAW, DAW 315 H, 500 H DAW
Magnesium hot chamber machine (DAM-F)
Frech is famous for the technical advances of the last minute. Do not copy others. Always innovating. Frech built the first machine casting hot chamber for magnesium in the world in 1966 and since then, we have demonstrated our capability in the manufacture of hot chamber machines up to 9300 kN:
- The continuous development of faster injection units
- Inductive heating nozzle and gooseneck for a casting process stable
|
|
DAM 80 F, 125 F DAM, DAM 200 F, 315 F DAM, DAM 500 F, 800 F DAM
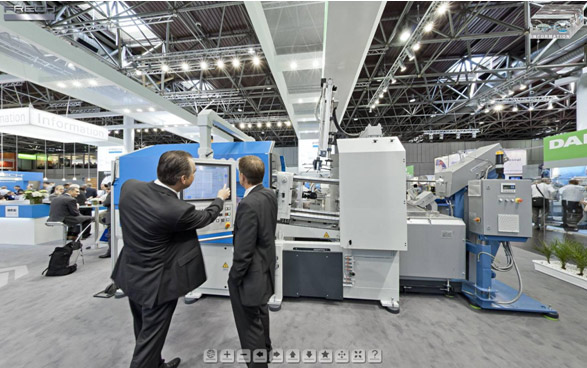
Prototypes: hot chamber injection of aluminum.
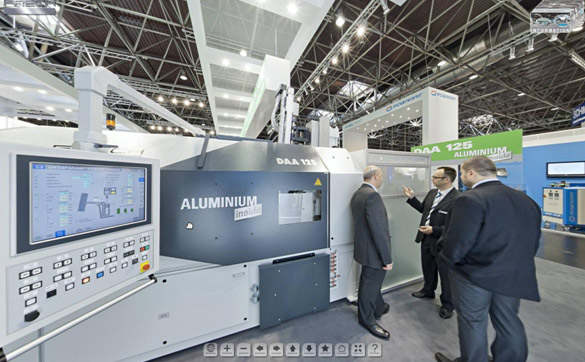
|